The world of 3D printing is scary. Words like CAD, slicer, and extrude are bound to intimidate hopeful hobbyists into fleeing from their new found interest. Fortunately, we here at Fluxspace are working to demystify that process for folks who aren’t quite ready to jump right into Solidworks to create a part for manufacturing with dissolvable filament and spiralized contours. One huge tool to do this has been ShapeDiver: the online platform that allows users to post Grasshopper scripts for use most commonly in e-commerce platforms.
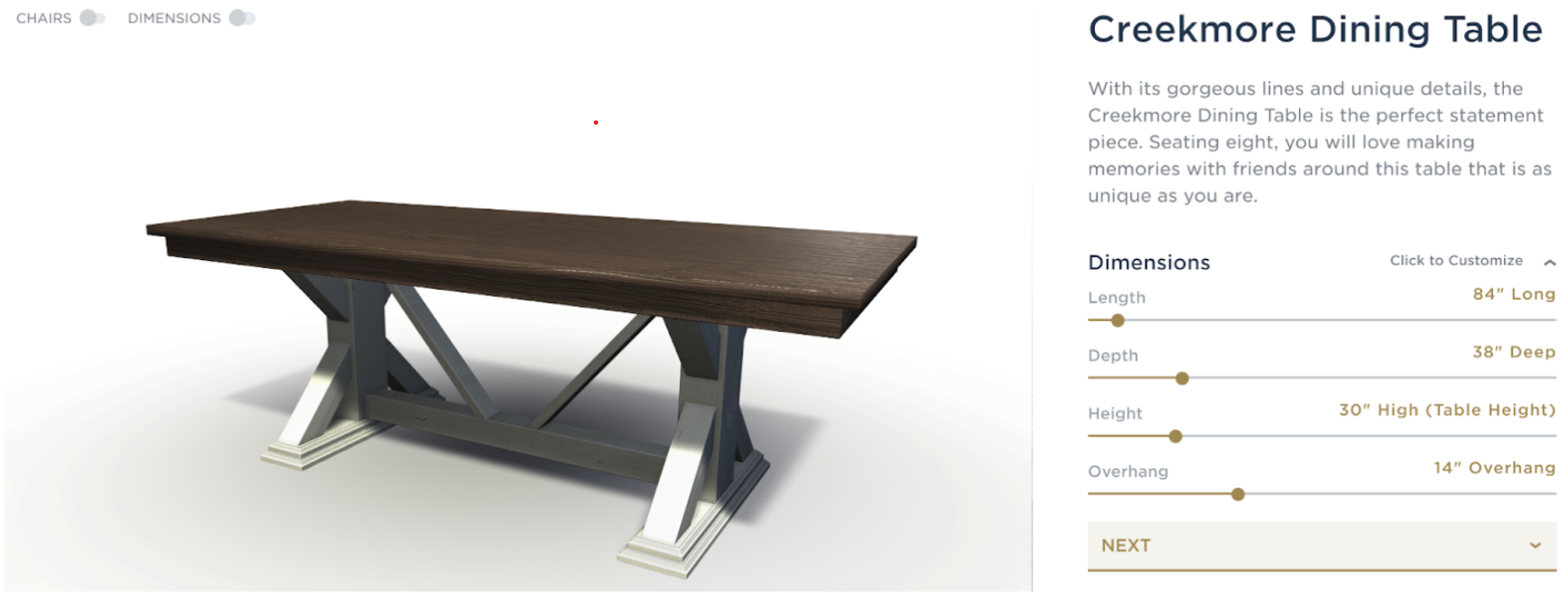
Before we continue, it needs to be made clear what exactly Grasshopper is. Grasshopper is a plugin for Rhino that enables designers to create parameterized CAD models that can quickly be regenerated and changed. For more information on this, check out my blog post introducing Grasshopper (it’s a banger).
ShapeDiver opens all sorts of doors for new-age design. From custom lamp shades, to specialized furniture, to orthopedic inserts, ShapeDiver helps companies to provide customers with a truly unique experience surrounding production, additive manufacturing, and architecture. However, we at Fluxspace have our eyes on another horizon; we concern ourselves with the way people learn, and learning CAD is an invaluable skill for the 21st century. So, ShapeDiver gives us a new way to lay the building blocks of CAD for emerging engineers.
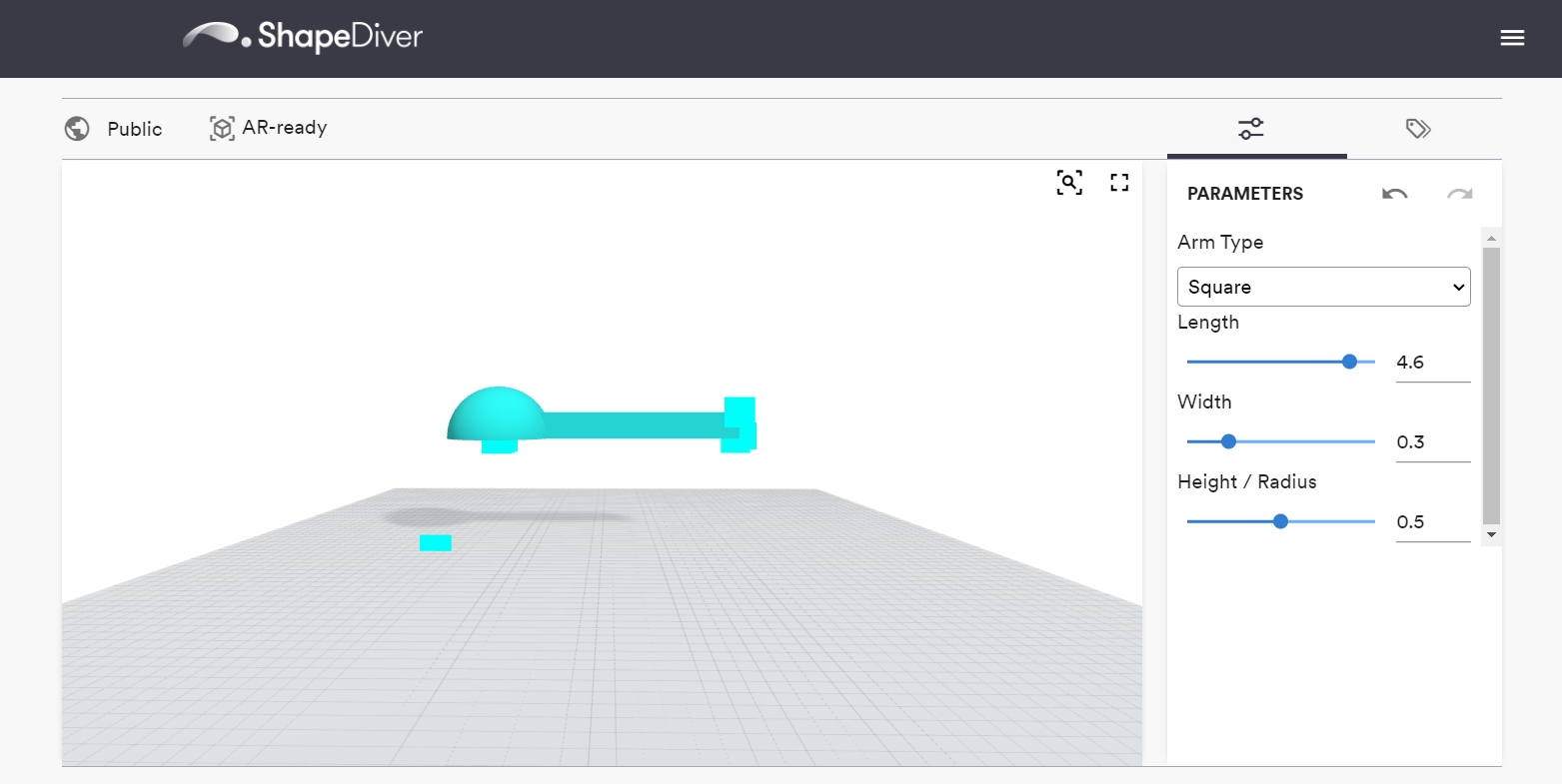
This catapult configurator is our very first ShapeDiver project. This is a great example of how ShapeDiver can be used to help students understand 3D modeling. We designed this catapult arm to be printed using Ninjaflex, also known as TPU (thermoplastic polyurethane), a flexible alternative to the traditional plastics we use in 3D printing like PLA. Ninjaflex is the perfect material for a catapult arm due to it's elasticity and resilience to fracture. Follow the link in Resources below to check out this configurator and explore the possibilities of ShapeDiver!
Project Examples
Have a solution to this challenge you want to share? Take a photo or video of your prototype, post it on social media, and don’t forget to tag us @fluxspace_io